The project for the development of adaptive 3D woven fiber-reinforced composite structures with high fatigue strength was motivated by the ever-increasing energy consumption of buildings. This is caused by climate change followed by increasing temperatures and a growing need for air conditioning of indoor spaces in combination with insufficient shading. In order to counteract the increasing energy consumption, new shading systems are needed that can regulate themselves continuously and are able to shade even complex façade geometries (modern architecture). This is where standardized façade shading systems reach their limits in terms of full area coverage and also fatigue strength, since conventional shading systems are based on rigid-body mechanisms that are connected to each other by mechanical joints. Exposed to environmental conditions, these joints can lead to high maintenance intensity due to friction and abrasion.
In biology, many approaches can be found for motion systems that work without any joints (cf. projects A03 and A04 as well as BIAG), which can be transferred to technical applications and thus lead to an overall more robust system. When integrating expanding pneumatic actuators into the layered structure, delaminations can occur in the fiber-reinforced composites, leading to an early failure of the adaptive component or to a change in its deformation properties. 3D weaving technology offers the possibility of integrating interlaminar connections between the individual layers of the fiber-reinforced composites by means of bindings in the fabric. This effectively prevents delamination in the actuation plane.
In the project FRP-hinges, an interdisciplinary team of architects, civil and textile engineers developed a fatigue-resistant multilayer fiber-reinforced composite hinge based on the above-mentioned approach. Within the project, another advantage of 3D weaving technology in relation to adaptive FRP components was demonstrated: The manufacturing time of the fiber-reinforced composite component is considerably reduced, since the time-consuming stacking process (single-ply lay-up) can be dispensed.. The mechanical and simulative analysis of different weaves and gradients in and at the transition of the moving flap to the hinge led to the development of a ±45° weave – implemented in this form for the first time on a 3D weaving machine. The project was concluded with the public presentation of the demonstrator.
Project Duration
August 2020 – November 2022
Project Team
DITF German Institutes of Textile and Fiber Research Denkendorf
Prof. Dr.-Ing. Götz T. Gresser, Dr.-Ing. Hans-Jürgen Bauder, Hermann Finckh, Florian Fritz, Felix Wollenhaupt
ITFT Institute for Textile and Fiber Technologies
University of Stuttgart
Prof. Dr.-Ing. Götz T. Gresser, Dr.-Ing. Larissa Born, Lena Schwill
ITKE Institute of Building Structures and Structural Design
University of Stuttgart
Prof. Dr.-Ing. Jan Knippers, Mona Mühlich, Axel Körner
Funding
The IGF project 21293 N of the Research Association Forschungskuratorium Textil e.V., Reinhardtstraße 14-16, 10117 Berlin was funded by the Federal Ministry of Economic Affairs and Climate Action via the AiF within the framework of the program for the promotion of joint industrial research (IGF) on the basis of a resolution of the German Federal Parliament.
Public Final Report
The final report of research project 21293 N is available from the German Institutes of Textile and Fiber Research Denkendorf (DITF).
Contact
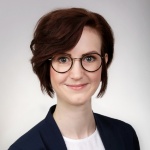
Larissa Born
Dr.-Ing.Deputy Director