2024
- Born, L., Gonzalez, S.M., Edith, A., Ridder, M., Körner, A.H., Knippers, J., Gresser, G.T.: FlectoSol - A pneumatically activable PV-functionalized faccade shading module with bending motion in two directions for solar tracking. Developments in the Built Environment. 18, 100372 (2024). https://doi.org/10.1016/j.dibe.2024.100372.
- Mindermann, P., Acker, D., Wegner, R., Fasoulas, S., Gresser, G.T.: Long-span fiber composite truss made by coreless filament winding for large-scale satellite structural systems demonstrated on a planetary sunshade concept. Scientific Reports. 14, 8190 (2024). https://doi.org/10.1038/s41598-024-58513-w.
2023
- Engert, M., Werkle, K.T., Wegner, R., Born, L., Gresser, G.T., Möhring, H.-C.: Validation of the Manufacturing Methodology of Prestressed Fiber-Reinforced Polymer Concrete by the Variation of Process Parameters. (2023). https://doi.org/10.3390/ma16237377.
- Gil Pérez, M., Mindermann, P., Zechmeister, C., Forster, D., Guo, Y., Hügle, S., Kannenberg, F., Balangé, L., Schwieger, V., Middendorf, P., Bischoff, M., Menges, A., Gresser, G.T., Knippers, J.: Data processing, analysis, and evaluation methods for co-design of coreless filament-wound building systems. Journal of Computational Design and Engineering. 1–35 (2023). https://doi.org/10.1093/jcde/qwad064.
- Gonzalez, E.A., Moser, S., Körner, A., Born, L., Gresser, G.T., Weitlander, R., Knippers, J.: Advancing solar control and energy harvesting through the use of pneumatically actuated elastic adaptive façades. In: Proceedings 10th ECCOMAS Thematic Conference on Smart Structures and Materials. pp. 744–756. Smart2023 (2023). https://doi.org/10.7712/150123.9828.444680.
- Maheswaran, T., Mindermann, P., Acker, D., Gresser, G.T., Fasoulas, S.: International planetary sunshade concept with a function-integrated and scalable support structure based on coreless filament winding. Journal of Physics: Conference Series. 2526, 012113 (2023). https://doi.org/10.1088/1742-6596/2526/1/012113.
- Moser, S., Gonzalez, E.A., Körner, A., Born, L., Gresser, G.T., Knippers, J., Weitlaner, R.: Datengesteuerte Regelungsstrategie mittels einer modellbasierten Evaluierung: Anwendung an einer adaptiven Fassade in Freiburg. In: Proceedings LICHT2023. Lichttechnische Gesellschaften Österreich, Deutschland, Niederlande und Schweiz in Partnerschaft mit FILD und LUXLUMINA (2023).
- Wegner, R., Engert, M., Gresser, G.T., Möhring, H.-C., Bonten, C., Kreutzbruck, M.: Structural Improvement of Mineral Cast through pre-stressed Carbon Fibre Reinforcements for Application in Machine Tool Construction. In: Bonten, C. and Kreutzbruck, M. (eds.) 28. Stuttgarter Kunststoffkolloquium. pp. 151--157. IKT Universität Stuttgart, Stuttgart (2023).
2022
- Jonas, F., Knippers, J., Gresser, G., Born, L., Milwich, M.: EP 3 460 114 B1 - FASERVERBUNDSTRUKTUR, VERZWEIGUNGSKNOTEN ZUM GEBÄUDEBAU SOWIE VERFAHREN ZUR HERSTELLUNG DES VERZWEIGUNGSKNOTENS ZUM GEBÄUDEBAU, https://worldwide.espacenet.com/patent/search/family/063442408/publication/EP3460114A2?q=18191052.2, (2022).
- Mindermann, P., Gil Pérez, M., Kamimura, N., Knippers, J., Gresser, G.T.: Implementation of fiber-optical sensors into coreless filament-wound composite structures. Composite Structures. 290, 115558 (2022). https://doi.org/10.1016/j.compstruct.2022.115558.
- Mindermann, P., Gresser, G.T.: Adaptive winding pin and hooking capacity model for coreless filament winding. Journal of Reinforced Plastics and Composites. (2022). https://doi.org/10.1177/07316844221094777.
- Mindermann, P., Müllner, R., Dieringer, E., Ocker, C., Klink, R., Merkel, M., Gresser, G.T.: Design of Fiber-Composite/Metal–Hybrid Structures Made by Multi-Stage Coreless Filament Winding. Applied Sciences. 12, 2296 (2022). https://doi.org/10.3390/app12052296.
- Mindermann, P., Pérez, M.G., Knippers, J., Gresser, G.T.: Investigation of the Fabrication Suitability, Structural Performance, and Sustainability of Natural Fibers in Coreless Filament Winding. Materials. 15, 3260 (2022). https://doi.org/10.3390/ma15093260.
- Mindermann, P., Witt, M.-U., Gresser, G.T.: Pultrusion-winding: A novel fabrication method for coreless wound fiber-reinforced thermoset composites with distinct cross-section. Composites Part A: Applied Science and Manufacturing. 154, 106763 (2022). https://doi.org/10.1016/j.compositesa.2021.106763.
2021
- Bodea, S., Mindermann, P., Gresser, G.T., Menges, A.: Additive Manufacturing of Large Coreless Filament Wound Composite Elements for Building Construction. 3D Printing and Additive Manufacturing. (2021). https://doi.org/10.1089/3dp.2020.0346.
- Mindermann, P., Bodea, S., Menges, A., Gresser, G.T.: Development of an Impregnation End-Effector with Fiber Tension Monitoring for Robotic Coreless Filament Winding. Processes. 9(5), 806 (2021). https://doi.org/10.3390/pr9050806.
- Mindermann, P., Rongen, B., Gubetini, D., Knippers, J., Gresser, G.T.: Material Monitoring of a Composite Dome Pavilion Made by Robotic Coreless Filament Winding. Materials. 14, 5509 (2021). https://doi.org/10.3390/ma14195509.
- Mühlich, M., Gonzales, E.A., Born, L., Körner, A., Schwill, L., Gresser, G.T., Knippers, J.: Deformation Behavior of Elastomer-Glass Fiber-Reinforced Plastics in Dependence of Pneumatic Actuation. Biomimetics. 6, 43 (2021). https://doi.org/10.3390/biomimetics6030043.
2020
- Born, L.: Grundlagen für die Auslegung und Gestaltung eines Hybridmaterials für außen liegende, adaptive Fassadenbauteile aus Faserverbundkunststoff, http://elib.uni-stuttgart.de/handle/11682/11150, (2020). https://doi.org/10.18419/OPUS-11133.
- Körner, A., Born, L., Bucklin, O., Suzuki, S., Vasey, L., Gresser, G.T., Menges, A., Knippers, J.: Integrative design and fabrication methodology for bio-inspired folding mechanisms for architectural applications. Computer-Aided Design. (2020). https://doi.org/10.1016/j.cad.2020.102988.
- Mindermann, P., Gresser, G.T., Milwich, M.: EP000003808547A1 - Method and tool arrangement for producing a fibre matrix composite profile structure and fibre matrix composite profile structure, (2020).
2019
- Born, L., Gresser, T., Milwich, M.: EP 3 552 807 A1 - FASERVERBUNDBAUTEIL, HYBRIDBAUTEIL UND VERFAHREN ZUM HERSTELLEN EINES FASERVERBUNDBAUTEILS, (2019).
- Born, L., Gresser, T., Milwich, M.: DE 10 2018 108 745 A1 - Faserverbundbauteil, Hybridbauteil und Verfahren zum Herstellen eines Faserverbundbauteils, (2019).
- Born, L., Körner, A., Mader, A., Schieber, G., Milwich, M., Knippers, J., Gresser, G.T.: Adaptive FRP Structures For Exterior Applications. Advanced Materials Letters. 10, 913–918 (2019). https://doi.org/10.5185/amlett.2019.0029.
- Bunk, K., Jonas, F.A., Born, L., Hesse, L., Möhl, C., Gresser, G.T., Knippers, J., Speck, T., Masselter, T.: From plant branchings to technical support structures. In: Knippers, J., Schmid, U., and Speck, T. (eds.) Biomimetics for Architecture: Learning from Nature. pp. 144–152. De Gruyter, Berlin, Boston (2019). https://doi.org/10.1515/9783035617917-019.
- Jonas, F., Knippers, J., Gresser, G., Born, L., Milwich, M.: EP 3 460 114 A2 - FASERVERBUNDSTRUKTUR, VERZWEIGUNGSKNOTEN ZUM GEBÄUDEBAU SOWIE VERFAHREN ZUR HERSTELLUNG DES VERZWEIGUNGSKNOTENS ZUM GEBÄUDEBAU, (2019).
- Jonas, F., Knippers, J., Gresser, T., Born, L., Milwich, M.: DE 10 2017 008 661 A1 - Faserverbundstruktur, Verzweigungsknoten zum Gebäudebau sowie Verfahren zur Herstellung des Verzweigungsknotens zum Gebäudebau, (2019).
- Kovaleva, D., Gericke, O., Wulle, F., Mindermann, P., Sobek, W., Verl, A., Gresser, G.T.: Rosenstein Pavilion: a lightweight concrete shell based on principles of biological structures. In: Knippers, J., Schmid, U., and Speck, T. (eds.) Biomimetics for Architecture: Learning from Nature. pp. 92–101. De Gruyter, Berlin, Boston (2019). https://doi.org/10.1515/9783035617917-012.
- Mader, A., Born, L., Gresser, T., Knippers, J., Milwich, M., Schieber, G., Müller, L., Körner, A.: EP 3 524 826 A1 - COMPONENT HAVING AN INTEGRATED ACTUATOR SYSTEM, (2019).
- Mader, A., Born, L., Gresser, T., Knippers, J., Milwich, M., Schieber, G., Müller, L., Körner, A.: DE 10 2018 103 178 A1 - Bauteil mit integrierter Aktuatorik, (2019).
- Mader, A., Born, L., Körner, A., Schieber, G., Masset, P.-A., Milwich, M., Gresser, G.T., Knippers, J.: Bio-inspired integrated pneumatic actuation for compliant fiber-reinforced plastics. Composite Structures. (2019). https://doi.org/10.1016/j.compstruct.2019.111558.
- Mindermann, P., Gresser, G.T., Milwich, M.: DE102019127568A1 - Verfahren und Werkzeuganordnung zum Herstellen einer Faser-Matrix-Verbund-Profil-Struktur und Faser-Matrix-Verbund-Profil-Struktur, (2019).
- Saffarian, S., Born, L., Körner, A., Mader, A., Westermeier, A.S., Poppinga, S., Milwich, M., Gresser, G.T., Speck, T., Knippers, J.: From Pure Research To Biomimetic Products: The Flectofold Facade Shading Device. In: Knippers, J., Schmid, U., and Speck, T. (eds.) Biomimetics for Architecture: Learning from Nature. pp. 42–51. De Gruyter, Berlin, Boston (2019). https://doi.org/10.1515/9783035617917-007.
- Westermeier, A., Poppinga, S., Körner, A., Born, L., Sachse, R., Saffarian, S., Knippers, J., Bischoff, M., Gresser, G.T., Speck, T.: No Joint Ailments: How Plants Move And Inspire Technology. In: Knippers, J., Schmid, U., and Speck, T. (eds.) Biomimetics for Architecture: Learning from Nature. pp. 32–41. De Gruyter, Berlin, Boston (2019). https://doi.org/10.1515/9783035617917-006.
- Wulle, F., Kovaleva, D., Mindermann, P., Christof, H., Wurst, K.-H., Lechler, A., Verl, A., Sobek, W., Haase, W., Gresser, G.T.: Nature As Source Of Ideas For Modern Manufacturing Methods. In: Knippers, J., Schmid, U., and Speck, T. (eds.) Biomimetics for Architecture: Learning from Nature. pp. 84–91. De Gruyter, Berlin, Boston (2019). https://doi.org/10.1515/9783035617917-011.
2018
- Bischoff, M., Sachse, R., Körner, A., Westermeier, A.S., Born, L., Poppinga, S., Gresser, G.T., Speck, T., Knippers, J.: Modeling and analysis of the trapping mechanism of Aldrovanda vesiculosa as biomimetic inspiration for façade elements. In: IASS Annual Symposium in Hamburg (2018).
- Born, L., Möhl, C., Milwich, M., Gresser, G.: Textile connection technology for interfaces of fibre reinforced plastic-concrete-hybrid composites. In: Hybrid 2018 in Bremen (2018).
- Jonas, F.A., Born, L., Möhl, C., Gresser, G.T., Knippers, J.: Towards branched supporting structures out of concrete-FRP composites inspired from natural branchings. In: IASS Annual Symposium 2018 in Boston (2018).
- Mindermann, P., Gresser, G.T.: Robotic 3D Deposition of Impregnated Carbon Rovings with Gradient Properties for Primary Structures. In: 69th International Astronautical Congress (2018).
- Möhl, C., Born, L., Jonas, F.A., Gresser, G.T., Knippers, J., Hausmann, J.M., Siebert, M., von Hehl, A.: Manufacturing of branched structures for fibre-reinforced plastic-concrete-hybrid composites. In: Hybrid 2018 in Bremen. p. pp 165-170. (2018).
- Schieber, G., Born, L., Bergmann, P., Körner, A., Mader, A., Saffarian, S., Betz, O., Milwich, M., Gresser, G.T., Knippers, J.: Hindwings of insects as concept generator for hingeless foldable shading systems. Bioinspiration & Biomimetics. 13, (2018). https://doi.org/10.1088/1748-3190/aa979c.
2017
- Born, L., Körner, A., Schieber, G., Westermeier, A.S., Poppinga, S., Sachse, R., Bergmann, P., Betz, O., Bischoff, M., Speck, T., Knippers, J., Milwich, M., Gresser, G.T., Herrmann, A.: Fiber-reinforced plastics with locally adapted stiffness for bio-inspired hingeless, deployable architectural systems. Presented at the (2017). https://doi.org/10.4028/www.scientific.net/KEM.742.689.
- Bunk, K., Jonas, F.A., Born, L., Gresser, G.T., Knippers, J., Speck, T., Masselter, T.: Vom Ast zum Palast. In: Stuttgarter Beiträge zur Naturkunde, Serie C (2017).
- Körner, A., Born, L., Mader, A., Sachse, R., Saffarian, S., Westermeier, A.S., Poppinga, S., Bischoff, M., Gresser, G.T., Milwich, M., Speck, T., Knippers, J.: Flectofold - A biomimetic compliant shading device for complex free form facades. Smart Materials and Structures. 27, (2017). https://doi.org/10.1088/1361-665X/aa9c2f.
- Westermeier, A.S., Poppinga, S., Körner, A., Sachse, L., Knippers, J., Born, L., Bischoff, M., Gresser, G.T., Speck, T.: Keine Gelenkbeschwerden – Wie Pflanzen sich bewegen und die Technik inspirieren. In: Begleitband Baubionik-Ausstellung Naturkunde Museum Stuttgart Rosenstein (2017).
- Wulle, F., Kovaleva, D., Christof, H., Wurst, K.-H., Lechler, A., Verl, A., Sobek, W., Haase, W., Gresser, G.: Die Natur als Ideengeber für moderne Fertigungstechniken. In: Begleitband Baubionik-Ausstellung Naturkunde Museum Stuttgart Rosenstein (2017).
2016
- Born, L., Westermeier, A.S., Gresser, G.T., Poppinga, S., Speck, T.: Catching inspiration from the carnivorous plant Aldrovanda vesiculosa – Biological Role Model of the Shading System “Flectofold.” In: 8. Bremer Bionik-Kongress, Bremen (2016).
- Born, L., Jonas, F.A., Bunk, K., Masselter, T., Speck, T., Knippers, J., Gresser, G.T.: Branched Structures in Plants and Architecture. In: Biomimetic Research for Architecture and Building Construction. pp. 195–215. Springer, Cham (2016). https://doi.org/10.1007/978-3-319-46374-2_10.
- Christof, H., Milwich, M., Gresser, G.T.: Räumlich gekrümmte Pultrusionsprofile durch UV-aktive Harze. In: 24. Stuttgarter Kunststoffkolloquium. pp. 209–212 (2016).
- Coupek, D., Kovaleva, D., Christof, H., Wurst, K.-H., Verl, A., Sobek, W., Haase, W., Gresser, G.T., Lechler, A.: Fabrication of Biomimetic and Biologically Inspired (Modular) Structures for Use in the Construction Industry. In: Biomimetic Research for Architecture and Building Construction. pp. 319–339. Springer, Cham (2016). https://doi.org/10.1007/978-3-319-46374-2.
- Poppinga, S., Körner, A., Sachse, R., Born, L., Westermeier, A., Hesse, L., Knippers, J., Bischoff, M., Gresser, G.T., Speck, T.: Compliant Mechanisms in Plants and Architecture. In: Biomimetic Research for Architecture and Building Construction. pp. 169–193. Springer, Cham (2016). https://doi.org/10.1007/978-3-319-46374-2_9.
Contact
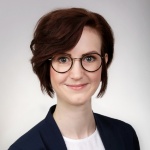
Larissa Born
Dr.-Ing.Deputy Director