Technologies for semi-finished products
Processing technologies
Technologies for semi-finished products
Fiber placement and winding
Fiber placement is an (automated) method for manufacturing fiber-reinforced composite structures. This process involes placing of rovings under tension in a specific lay-up pattern on a frame or core. Thus, planar, shell or tubular components can be created quickly and inexpensively. Depending on the shape of the core, more complex forms are possible. This method is often used for high performance structures where the fiber path is designed to be precisely laid down in accordance to the major (local) load conditions. Rovings for example made of glass or carbon impregnated with resin are placed onto the frame or core. Depending on the resin system and its parameters, it is cured in an oven or at room temperature.
Tufting
Based on the tufting technology known from carpet industry respectively z-reinforcement of textile stacks, a new method for joining fiber-reinforced composite components has been developed: Reinforcement pins made by tufting. Fiber loops are automatically introduced into the preform during production with a six-axes-robot-compatible tufting head. After the simultaneous consolidation of preform and loops, pins protrude from the component or into the void of a hollow component. The connection of two components or filling of a hollow component with a shrinking material is thus possible using both frictional connection and form fit.
Weaving
With a new shuttle weaving technology it is possible to produce endless fiber-reinforced, multi-layered, two-dimensional and three-dimensional structures in near-net shape geometry. A 3D weaving machine from MAGEBA is available for this purpose, on which simulative supported, load-path adapted components can be produced.
Processing technologies
3D Printing
UV-Curing
UV radiation is an alternative to thermal resin curing. A photoinitiator is added to the resin formulation, which is reactive for a particular ultraviolet wavelength range. The LED spotlight enables the immediate curing of structures, high production rates and controllability at the same time.
Vacuum Infusion
In addition to hand lamination technology, experimental components (small- and large-scale) with thermosetting matrix systems can be produced quickly and cost-efficient by various infusion techniques. A one-sided mold allows complex and large component geometries to be manufactured in a comparatively simple process.
Togehter with DITF Denkendorf, ITFT is developing new technologies for the production of semi-finished textiles and fiber-reinforced composites.
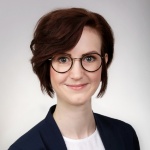
Larissa Born
Dr.-Ing.Deputy Director