The research project VFMG 2.0 focuses on the development and optimization of prestressed fiber-reinforced mineral cast (VFMG) for highly stressed structural components in machine tool construction. Based on the results of the previous project VFMG 1.0, the focus of VFMG 2.0 is on the further development of the material composition for the analysis of residual stresses and residual stress fields generated by the prestressing of carbon fiber rovings. The goal is to strategically adjust these residual stresses to meet specific load requirements. In addition, the manufacturing process is systematically optimized to investigate the interaction between manufacturing parameters and the resulting mechanical properties. Special emphasis is placed on the development of a roving layup process that enables the efficient integration and prestressing of carbon fiber rovings into the mineral casting matrix, thus facilitating the production of geometrically complex and load path optimized components.
Another critical aspect of the project is the development of numerical simulation models that accurately represent the behavior of the hybrid material. These models take into account the interaction between the mineral cast matrix and the embedded carbon fiber rovings, as well as the residual stresses induced by prestressing. They serve as a basis for the load-optimized design of structural components specifically tailored to the requirements of advanced machine tool construction.
By combining material development, process optimization and simulation, the aim is to produce high-performance yet resource-efficient components that set new standards in terms of stability and lightweight design. To demonstrate this potential, the project will conclude with a topology-optimized component at demonstrator level.
Project Duration
March 2025 – Feburary 2028
Project Team
ITFT Institute for Textile and Fiber Technologies, University of Stuttgart
Prof. Dr.-Ing. Götz T. Gresser, Dr.-Ing. Larissa Born, Robert Wegner
IfW Institute for Machine Tools, University of Stuttgart
Prof. Dr.-Ing. Hans-Christian Möhring, Kim Torben Werkle, Michelle Engert
Funding
This research project is funded by the German Research Foundation (DFG, Deutsche Forschungsgemeinschaft) – Project number 451783369
Contact
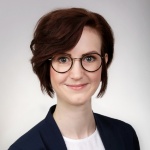
Larissa Born
Dr.-Ing.Deputy Director